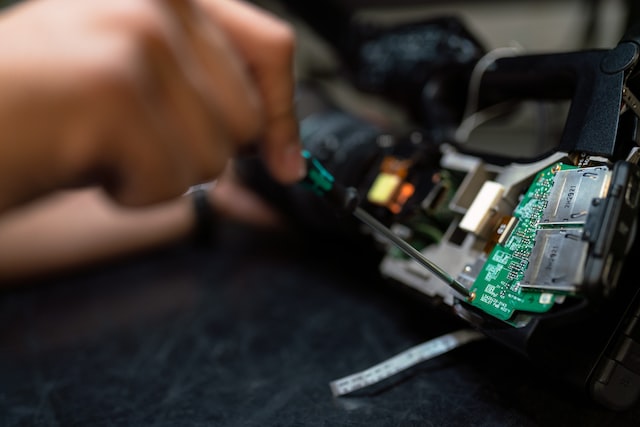
Since the industrial revolution, maintaining engineering systems has been a constant challenge. Despite a large number of technological advances, equipment maintenance remains a challenge due to a large number of factors to take into account. Among these, we find complexity, costs, and competition. Every year billions of dollars are invested in industrial maintenance equipment in the world. So, from this need, various maintenance strategies have emerged. For example, predictive, preventive, reactive, and corrective maintenance, among others. This time, we focus on predictive maintenance features.
The need for maintenance
The beginning of maintenance engineering was born due to the need to have the equipment working properly. So, we can attribute the beginning of maintenance engineering to the invention of the steam engine, created by James Watt (1736-1819) in 1769, in Great Britain. Naturally, every machine tends to fail. This factor remains to this day, despite technological advances. Also, we have the factor of human interaction. This can be seen during design, installation, production, and even maintenance. Although the degree of interactions may vary from product to product, they are subject to deterioration by human error.
Predictive maintenance is becoming more and more entrenched in companies, especially those that have multiple processes and machinery. This procedure makes it possible to avoid errors that could lead to large financial losses in devices like Atlas Copco LE5 Compressor.
In this article, we will talk about some of the advantages and disadvantages of this type of maintenance, which tends to anticipate possible errors, and we will compare it with corrective maintenance and preventive maintenance to learn about its differences and main characteristics. Do you want to specialize in this field of industry? Just keep reading!
What is predictive maintenance?
Predictive maintenance is a procedure that uses data analysis techniques and tools to previously detect anomalies in equipment and work processes. In this way, these problems can be solved before there is a failure. That is, thanks to this type of maintenance, errors in the system can be predicted.
Predictive maintenance has three key components:
– Sensors and interconnected devices. At all times they send data on the performance and general status of the machine.
– Cloud storage solutions and software. This allows for storage and analysis of this data reflected in sensors and devices.
– Processed data. The information is collected to establish comparisons and patterns and make predictions.
Advantages and disadvantages
This predictive data analysis technique has advantages and disadvantages, as we see below.
Some of the advantages are:
– The useful life of the machinery and its components is increased.
– Reduction of maintenance costs both for the hours of work and for the parts acquired for the repair.
– Maximizes the productivity of components and machinery to increase performance at a lower cost.
– Improves the safety of machinery and workers.
Among the disadvantages we find:
– A higher job qualification is required to analyze the data.
– It involves a large initial investment for diagnosis.
– It requires alignment in the company to carry out the management and analysis.
Differences between predictive, preventive, and corrective maintenance
We have seen what predictive maintenance is and how to apply it to industrial automation. But how is it different from preventive maintenance and corrective maintenance?
If predictive maintenance consists of data analysis to anticipate the problem, corrective maintenance is the opposite. It is also called reactive or breakdown and is done when there is already a failure and the equipment must be repaired. It is most often used in the motor industry. The repair is done when the problem is already there. In this case, the derived costs are higher; production can be stopped, it negatively impacts finances, and repair time can be increased.
As for preventive maintenance, this is based on a periodic check of the machinery to anticipate errors regardless of whether it is required. It also consists of a review if any symptoms are detected. In other words, the difference with the predictive procedure is that the investment is also higher as the equipment has to be checked continuously. This will entail more labor costs and the purchase of parts by not having programming as you have with the predictive. An example can be the traditional newspaper industry and printing houses, where there are continuous checks to locate some errors.